Supply Chain Automation for a Global Equipment Manufacturer
Client
The client is a manufacturer of equipment that requires raw materials located across their facilities. They transfer these raw materials from a facility in the US to their manufacturing location in Asia.
The Project Scope
Transferring the material between the two locations is a multistep process that involves determining the demand, checking for inventory, creating a purchase order, and finally a shipping label to send the consignment. Every day, multiple people from the planning department are responsible for executing this manual process and validating the work.
CLIENT PROFILE
EMPLOYEES: 1,400+
INDUSTRY: Manufacturing – Durables
HEADQUARTERS: Massachusettes
FOUNDED: 1950
The painstaking process was a prime candidate for automation, therefore Smartbridge set forth in designing and developing a solution with Robotic Process Automation(RPA). The manufacturer wanted to see these milestones hit by implementing RPA:
The Smartbridge Solution
Smartbridge devised a bot that would create the purchase orders and the shipping labels needed to perform the transfer of the raw materials overnight. In the morning, the planners would have the required documents printed and ready for them to review.
Here’s a look at the steps the bot takes to execute the inventory transfer process:
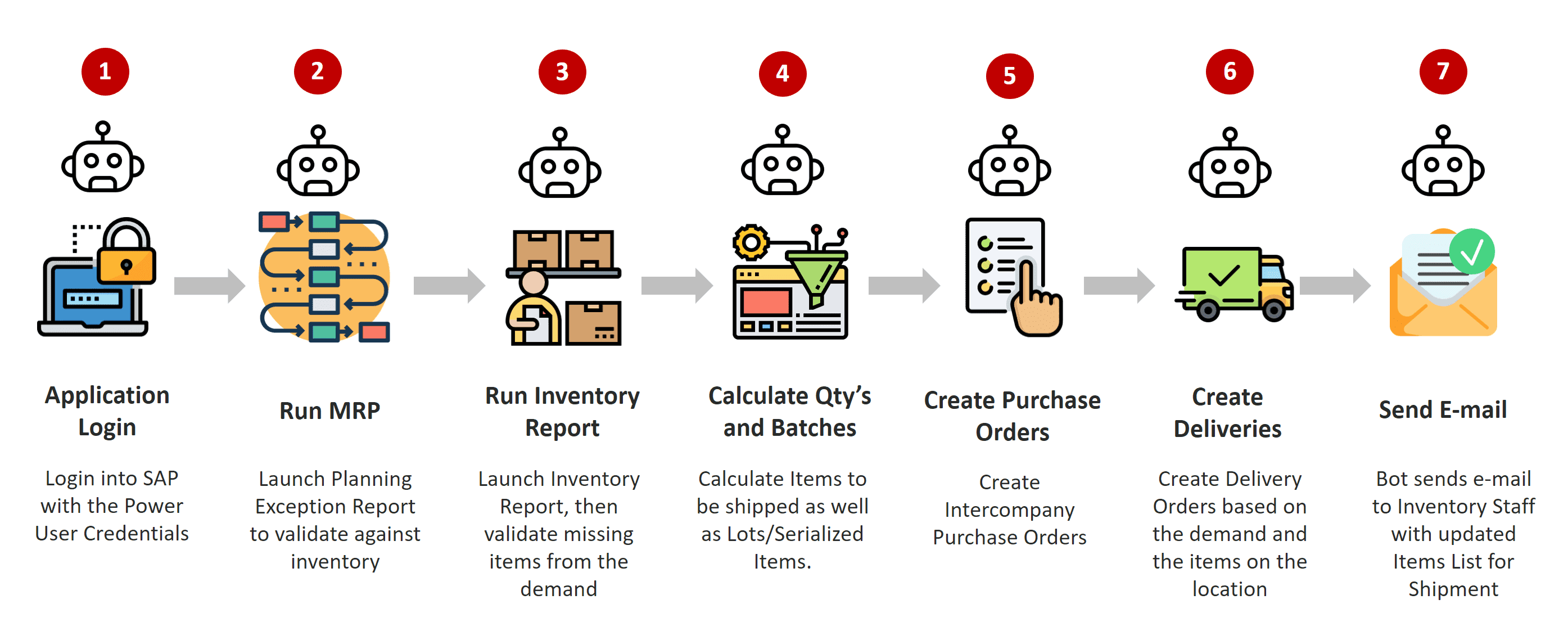
Vendor Selection
The client decided UiPath would give them the best chance of success. Smartbridge then assisted with the UiPath environment installation and configuration. We also delivered process documentation based on pre-designed templates.
The technology stack required to accomplish this project included UiPath, SAP, and Microsoft Excel.
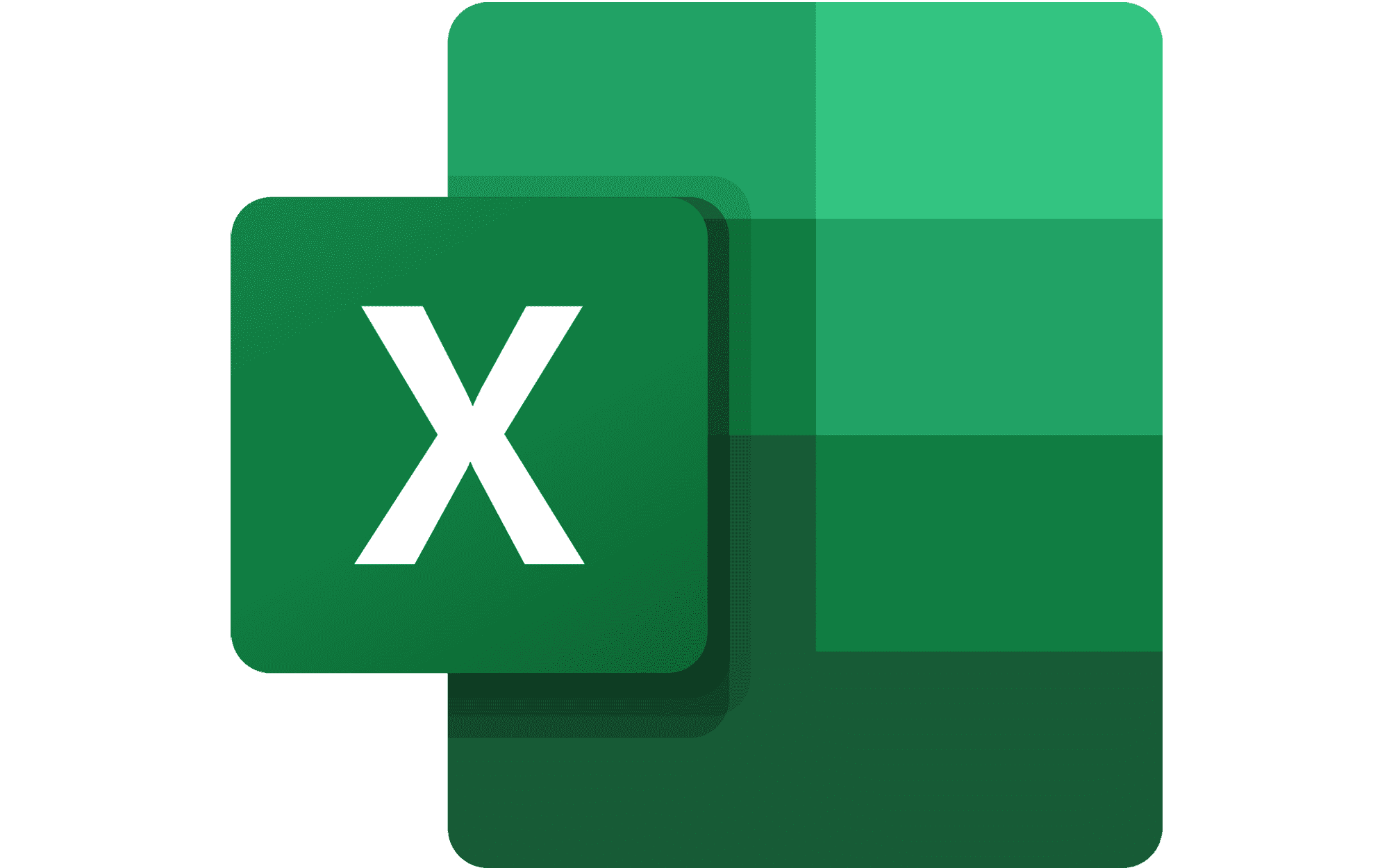
Success Through an Automation Implementation
The manufacturing client was excited to see that the end-to-end process was completely automated with no need for a manual intervention! In fact, human errors associated with creating the POs and shipping labels were eliminated.
The execution time spent on inventory movement and validation was ultimately reduced by 82%, eliminating nearly 60 hours of monthly work. Additionally, the planner’s time, which was spent in manually intensive tasks, was made available for higher-value activities.
There’s more to explore at Smartbridge.com!
Sign up to be notified when we publish articles, news, videos and more!
Other ways to
follow us: