Data Entry Automation for a Medical Device Manufacturer
Smartbridge implemented a data entry automation for a medical device manufacturer to reduce their massive backlog of device implant warranty cards. With this automation solution in place, the manufacturer is experiencing an error rate reduction of 92% while freeing up over 4,320 man hours to reallocate to more revenue-driving opportunities.
Client
This billion-dollar client is a medical device manufacturing company that specializes in devices used for cardiac surgery and neuromodulation. Their devices and therapies are used worldwide, and they have a presence in more than 100 countries, employing 4,000+ people.
Project Scope
The device implant warranty card serves multiple purposes:
When health care providers place a medical device inside a patient, they fill out an implant card containing the device information, patient information, physician information, and procedure information. These physical, implant warranty cards are scanned and electronically sent to the manufacturer.
Our client wanted to explore and leverage Robotic Process of Automation (RPA) to automate the process of capturing implant card data into their device tracking database. The objectives of this automation project include:
Key Challenges
The client wanted to put an automation solution in place due to the overwhelming backlog of implant card entries that needed to be entered into the system. Once the information is entered into the system, the manufacturer warranty for the respective implanted device becomes active.
The client has 4 full-time employees solely dedicated to entering the data into their manufacturing database, and over 1,000 backlog implant cards to be entered into the system. If the data was not completely filled in on the received implant card, the employee has to request device and patient information from multiple departments and applications. To process the implant card, the employee needs to perform over 40 plus steps in 5 different applications.
In addition to the massive backlog they had on hand, it would require 3,208 manual hours to complete. That’s without entering the 350 implant cards the client receives on a weekly basis. Most importantly, patients rely on this client’s manufacturing warranty to be active as soon as it is implanted, not a year after the procedure.
The Smartbridge Solution
Smartbridge developed a solution for automating the 40 plus step process leveraging the client’s current tech stack with the addition of UiPath to automate the data entry, research, assigning, and uploading of the implant cards.
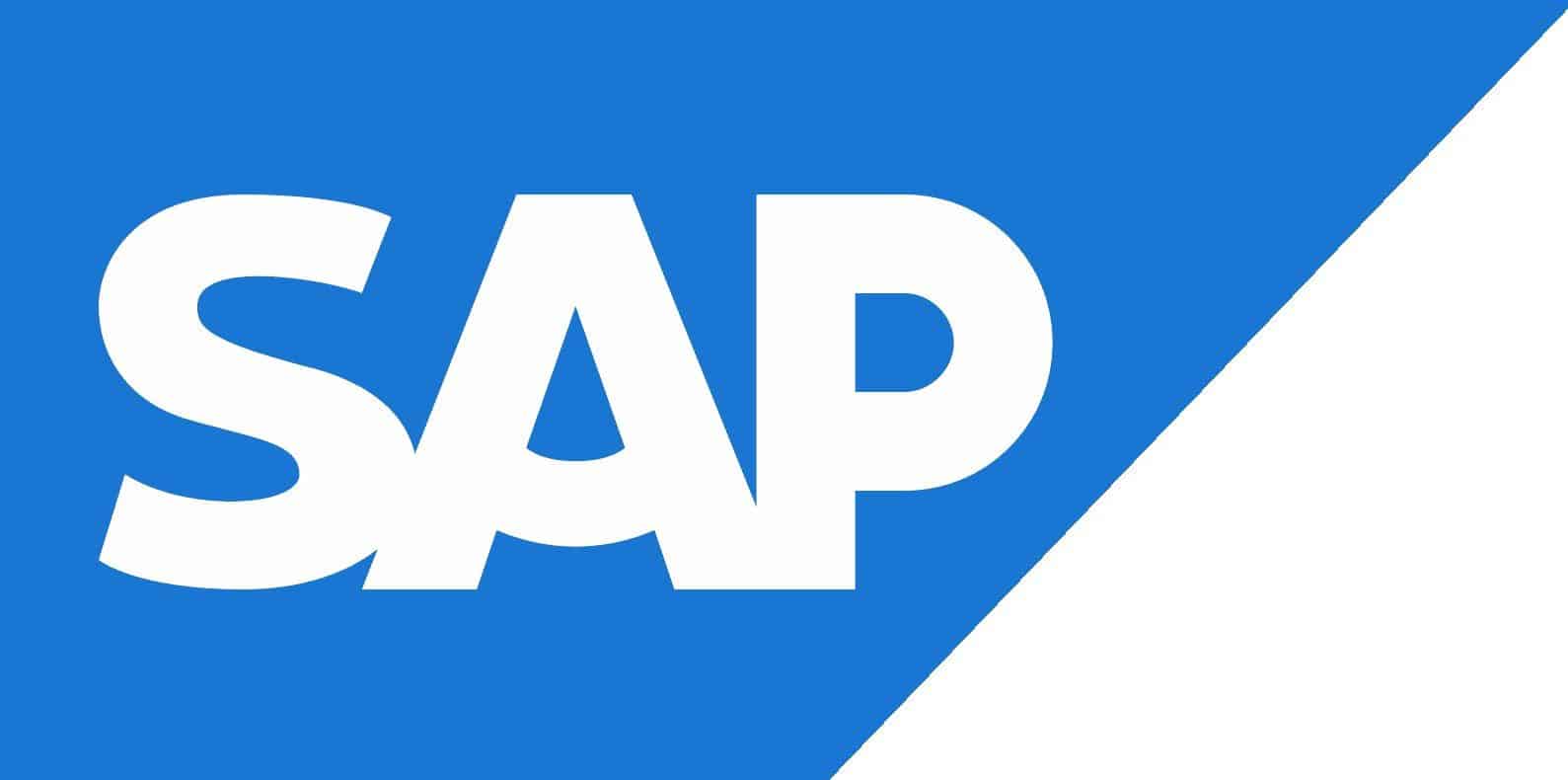
With the data entry automation in place, the employees work in tandem with the bots to save thousands of hours of manual data entry and research. They work alongside the bots to process each implant card at the initial stage of the process and at the final stage of the process.
To ensure data accuracy, the employee views the scanned implant cards and translates the information into text. After that, the bot takes over locating the medical device within their other enterprise systems and searches for any missing patient information from the implant cards. Once all the information is consolidated, the bot enters the implant card information into the device tracking module of the ERP system. In addition to completing the data entry, the bot also uploads all the implant card images to a shared location for auditing purposes. At the end of the process, a human now validates the data and resolves any errors.
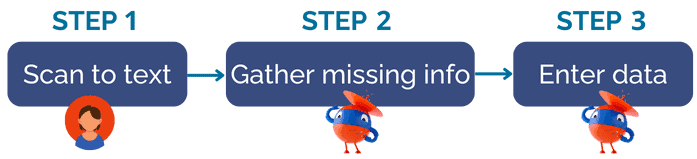
Now, with this data entry automation in place, the bot takes a heavy load off of the 40-plus processes and:
Success Through a Modernized Implementation
Smartbridge delivered a robust automation for the handling of the manufacturer’s implant device warranty cards, creating valuable impact for the client.
Device Data Entry Automation: Success By the Numbers
3
bots
deployed
18,200
device warranty cards
processed annually
4,320+
hours
reallocated annually
92%
improvement
over manual data entry
Now, since there are multiple bots deployed, there is no longer a backlog of warranty cards that need to be processed. The employees now have over 4,320 hours given back in their year to focus on revenue-generating opportunities and more strategic tasks.
Keep Reading: Global Real Estate Firm’s AP Invoice Automation
There’s more to explore at Smartbridge.com!
Sign up to be notified when we publish articles, news, videos and more!
Other ways to
follow us: